Pumbaa 66/123kW Central E-axle for electric 4.5T-6.0T logistics vehicle / 6m bus
Pumbaa PMEA5300ZCentral E-axle Technical parameters
Rated axle load(kg) |
3500 |
Axle housing forming method |
Stamping and welding |
Housing cross-section(mm) |
105×105×6 |
Top speed(km/h) |
100 |
Reduction ratio |
16.6 |
Nominated/peak output torque(Nm) |
135/320 |
Rated/peak power(kw) |
66/123 |
Maximum speed(rpm) |
12000 |
Motor dimensions(mm) |
Φ275×280 |
Leaf spring mounting distance(mm) |
952 |
Rim mounting distance(mm) |
1555 |
Overall width(mm) |
1757 |
Brake Specifications (Air Brake) |
Drum pose:φ310×100 |
Maximum braking torque(0.6MPa) |
2×5200Nm |
Wheel bolt specifications |
12-M22×1.5 |
Wheel bolt distribution circle diameter (mm) |
Φ222.25 |
Locate the stop(mm) |
Φ160.8 |
Assembly weight (kg) |
310 |
description2
Key Technology of Electric Drive Axle: Lightweight. High reliability. High Performance Materials
With the rise of electric and hybrid vehicles, electric axle technology is also gradually being introduced in the heavy-duty truck sector to achieve a more efficient and environmentally friendly mode of transportation. However, the weight of the integrated electric axle of heavy trucks is close to 1 ton, which poses new challenges to ride comfort and handling stability. Therefore, lightweight has become a key issue in the electric axle technology of heavy trucks;
With the increasing awareness of environmental protection and the requirement for fuel economy, the market demand for electric and hybrid vehicles is growing. As the main force in the field of commercial transportation, heavy-duty trucks also need to follow this trend and introduce more advanced power technology. As the core component of the powertrain of heavy trucks, the weight and performance of the electric axle are crucial to the overall performance of heavy trucks. Therefore, lightweight technology has become a key issue in the development of integrated electric axles for heavy trucks.
Lightweight design: Lightweight design is the foundation and key to realizing the lightweight of heavy-duty truck electric drive axles. Dimensional optimization, morphology optimization and structural optimization are important means of lightweight design. Dimensional optimization reduces weight by reducing the size of the part while ensuring the strength and stiffness of the part. Topography optimization improves the lightweighting effect of the part by changing the shape and profile of the part. Structural optimization reduces weight by optimizing the structure and layout of parts. These design methods need to be implemented with the help of tools such as computer-aided design and simulation analysis.
Lightweight materials: Lightweight materials play a key role in the lightweight of electric axles for heavy-duty trucks. Commonly used lightweight materials include high-strength steel, aluminum alloys, magnesium alloys, non-metallic materials and composite materials. High-strength steels can reduce the thickness and weight of parts without sacrificing strength. Aluminum alloys and magnesium alloys have low density and good processing properties, and can be used to make parts with light weight and high strength. Non-metallic materials such as plastics and fiber-reinforced composites have low density and good comprehensive properties, and are suitable for manufacturing some non-structural parts.
Lightweight manufacturing: Lightweight manufacturing is the key link to realize the lightweight of heavy-duty truck electric drive axles. New manufacturing processes such as thermoforming, laser tailored welding, roll forming, and hydroforming enable efficient manufacturing and lightweighting of complex-shaped parts. The thermoforming process can be used to complicate and lighten the shape of parts by heating and forming. Tailored laser welding can make multiple parts join precisely, reducing the amount of welding material used and the weight of the parts. Roll forming and hydroforming can produce large-size, high-strength parts by continuous forming, reducing the use of welded joints.
Balance between lightweight and cost control: The degree of lightweight needs to comprehensively consider material costs, production costs and performance requirements. In addition to weight reduction, it is also necessary to ensure the safety, NVH (noise, vibration, and stiffness) performance and durability of heavy-duty truck e-axles. As a result, lightweight design, lightweight materials, and lightweight manufacturing require a reasonable trade-off between cost and performance. Optimum performance of heavy-duty truck e-axles can only be achieved with minimal cost, weight and process investment.
Key Technology of Electric Drive Axle - High reliability
In terms of reliability work, we need to define the durability conditions of the electric axle based on the user's usage data. By collecting data on the actual usage and operating conditions of the user, we are able to better understand the working state of the e-axle under different conditions, and define the durability condition accordingly. This helps to optimize the structural design of the e-axle and ensures its reliability during the endurance road test of the vehicle assembly.
Secondly, in order to meet the challenges of design integration of diversified test contents brought about by high integration, we need to comprehensively consider multiple aspects such as electronic control, motor, gearbox and axle. The high level of integration makes these components tightly bound together, and the influence and coupling between them are more complex. Therefore, we need to design a comprehensive series of tests to comprehensively evaluate the performance and reliability of the e-axle under various operating conditions.
In addition, the deep platform design is also one of the keys to improving the reliability of the e-axle. The requirements for the use of e-axles may vary from vehicle to vehicle type, so the compatibility of this composite use needs needs to be taken into account during the design process. By adopting a unified platform design scheme, it can better meet the needs of different models and improve the versatility and reliability of the electric drive axle.
Key Technology of Electric Drive Axle - High performance materials
In electric axles, the demand for high-performance materials is also increasing, and key technologies and materials such as high-speed, high-insulation and high-temperature bearings, long-life high-insulation magnet wires, and high-performance silicon steel sheets play a vital role.
With the development of high-speed and high-voltage electric vehicle motors, bearings are facing problems such as wear and shaft current corrosion during the working process of the motor. To solve these problems, bearings need to have high speeds, high insulation, and high temperature resistance. To achieve this, we need to focus on key issues such as high-strength retainer technology and insulation technology.
Research on high-strength retainer technology is aimed at improving the load-bearing capacity and anti-wear performance of bearings. By optimizing the structural design and material selection of the retainer, the strength and wear resistance of the bearing can be improved, so as to meet the needs of high-speed motors.
The research of insulation technology aims to improve the insulation performance of bearings and prevent the occurrence of shaft current corrosion problems. In an electric drive system, due to the electromagnetic field generated when the motor is operating, the bearing may become a channel for electric current, resulting in shaft current corrosion. Therefore, we need to look for highly insulating materials and insulation technologies to improve the insulating ability of bearings and protect them from shaft current corrosion.
Key Technology of Electric Drive Axle - Lightweight
With the increasing awareness of environmental protection and the requirement for fuel economy, the market demand for electric and hybrid vehicles is growing. As the main force in the field of commercial transportation, heavy-duty trucks also need to follow this trend and introduce more advanced power technology. As the core component of the powertrain of heavy trucks, the weight and performance of the electric axle are crucial to the overall performance of heavy trucks. Therefore, lightweight technology has become a key issue in the development of integrated electric axles for heavy trucks.
Lightweight design: Lightweight design is the foundation and key to realizing the lightweight of heavy-duty truck electric drive axles. Dimensional optimization, morphology optimization and structural optimization are important means of lightweight design. Dimensional optimization reduces weight by reducing the size of the part while ensuring the strength and stiffness of the part. Topography optimization improves the lightweighting effect of the part by changing the shape and profile of the part. Structural optimization reduces weight by optimizing the structure and layout of parts. These design methods need to be implemented with the help of tools such as computer-aided design and simulation analysis.
Lightweight materials: Lightweight materials play a key role in the lightweight of electric axles for heavy-duty trucks. Commonly used lightweight materials include high-strength steel, aluminum alloys, magnesium alloys, non-metallic materials and composite materials. High-strength steels can reduce the thickness and weight of parts without sacrificing strength. Aluminum alloys and magnesium alloys have low density and good processing properties, and can be used to make parts with light weight and high strength. Non-metallic materials such as plastics and fiber-reinforced composites have low density and good comprehensive properties, and are suitable for manufacturing some non-structural parts.
Lightweight manufacturing: Lightweight manufacturing is the key link to realize the lightweight of heavy-duty truck electric drive axles. New manufacturing processes such as thermoforming, laser tailored welding, roll forming, and hydroforming enable efficient manufacturing and lightweighting of complex-shaped parts. The thermoforming process can be used to complicate and lighten the shape of parts by heating and forming. Tailored laser welding can make multiple parts join precisely, reducing the amount of welding material used and the weight of the parts. Roll forming and hydroforming can produce large-size, high-strength parts by continuous forming, reducing the use of welded joints.
Balance between lightweight and cost control: The degree of lightweight needs to comprehensively consider material costs, production costs and performance requirements. In addition to weight reduction, it is also necessary to ensure the safety, NVH (noise, vibration, and stiffness) performance and durability of heavy-duty truck e-axles. As a result, lightweight design, lightweight materials, and lightweight manufacturing require a reasonable trade-off between cost and performance. Optimum performance of heavy-duty truck e-axles can only be achieved with minimal cost, weight and process investment.
To sum up, lightweight, high-reliability and high-performance materials in the key technologies of electric axles have played a vital role in the development of electric vehicles. By researching key technologies and materials such as high-speed, high-insulation, high-temperature bearings, long-life high-insulation magnet wires, and high-performance silicon steel sheets, we can improve the performance and reliability of electric drive systems and promote the further development of electric vehicle technology. In the future, PUMBAA also needs to continuously strengthen research and innovation to improve the quality and efficiency of high-performance materials, and make greater contributions to the sustainable development of the electric vehicle industry.
Leave Your Message
Blog
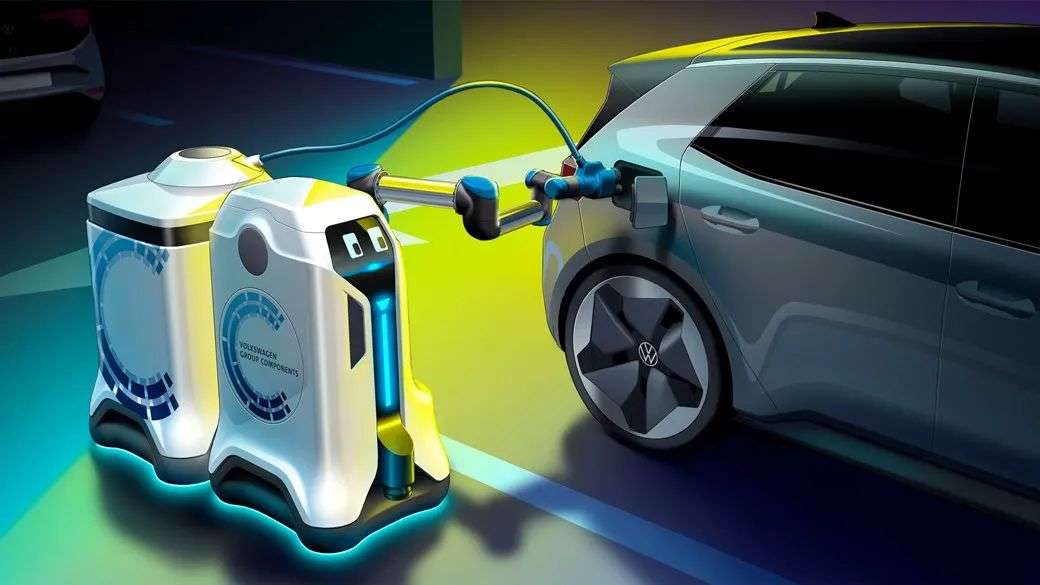
China’s getting a big electric car battery swapping boost in 2025. Would that work across the globe?
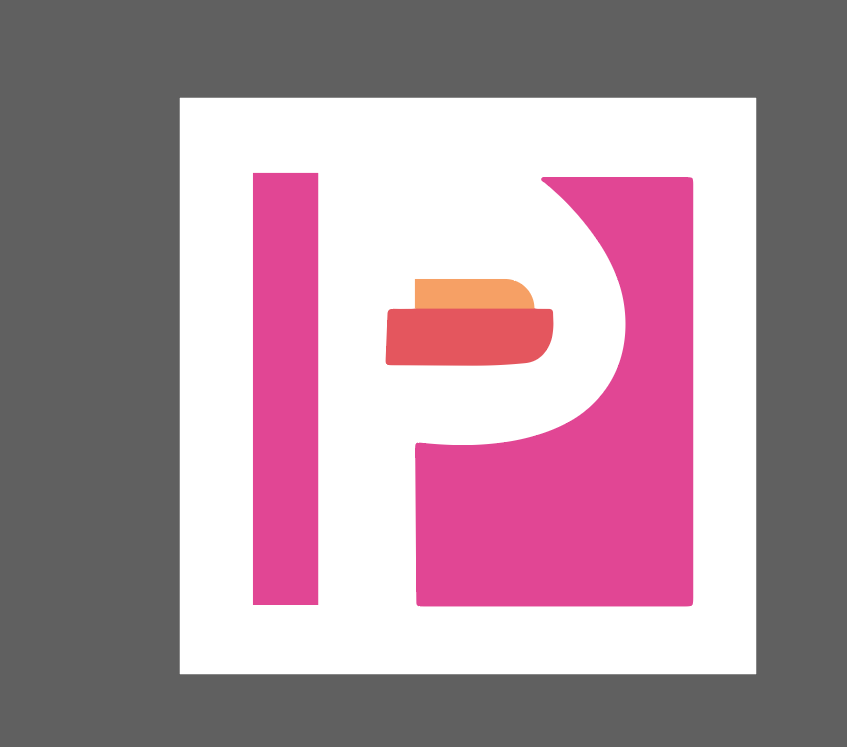
Pumbaa's Superior Electric Motor Service: Leading sales center for electric motors
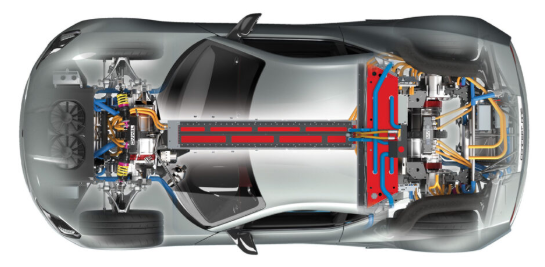
EVs Could Last Much Longer Than You Think
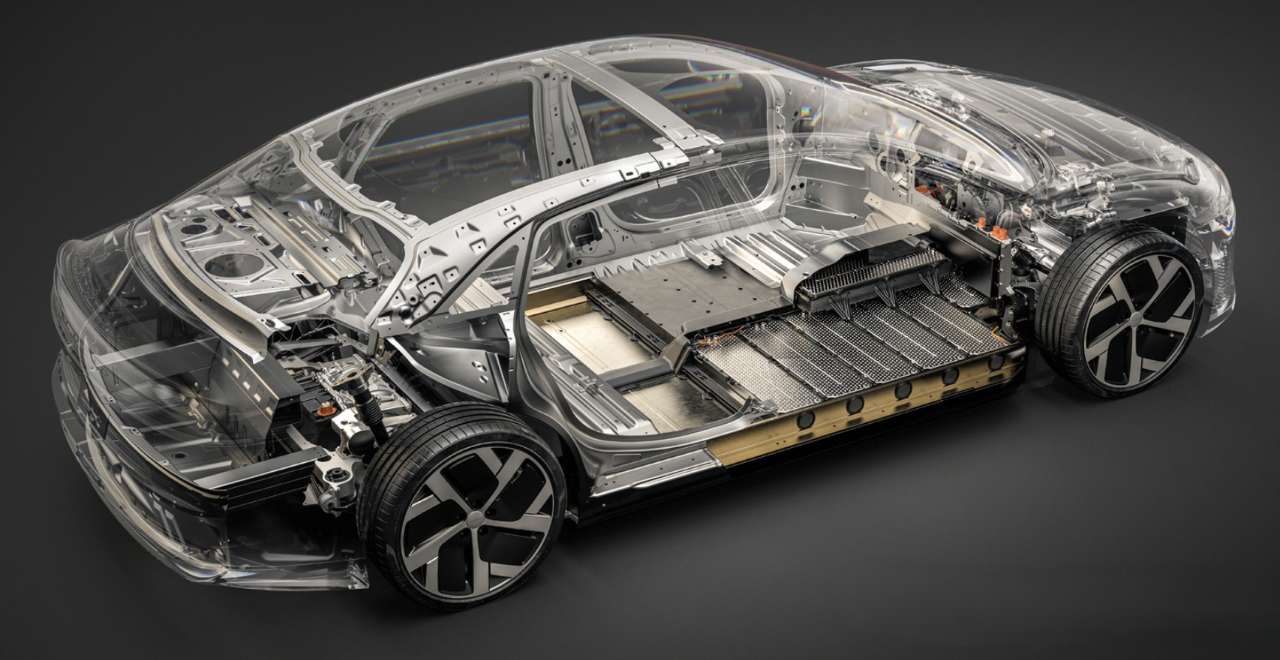